Buildings are often beautiful things, providing us with our daily environment in which we live, work, learn, and play. They also rely on a huge range of mechanical equipment, requiring regular maintenance to keep us comfortable, productive and safe.
The Safety in Design or ‘SID’ process is a mandatory component in the course of designing, constructing, operating, maintaining and commissioning our built world. SID provides a framework and risk assessment system that ensures human safety, and is at the forefront of how we interact with a building throughout its lifespan.
The SID process is a responsibility of all parties involved in the design and construction of a built asset. In partnership with the client, the design team and builder are all integral to a successful and safe outcome. Historically, we have occasionally witnessed a lack of understanding throughout the industry on how to implement safe, ongoing maintenance requirements into the final built outcome. This can culminate in the project containing unnecessary risks or operational tasks that could have been mitigated during the design stage.
A modern building is required to transfer data through kilometres of copper wire and fibre, transport water through intricate pipework, and relies on a vast array of mechanical systems to keep it performing at an optimal level. If one part of that ‘chain’ fails, it is important to be able to readily identify and fix the problem. However, if the client, owner or asset manager cannot access or rectify the problem safely, it can lead to damage or the need to relocate staff or tenants, meaning unexpected and unwanted costs and possibly lost income.
At the beginning of each project, the BADGE design team conducts a workshop to identify and understand potential project hazards. At this point, we apply the combined experience and knowledge of our construction teams and design personnel to determine how to eliminate risk or provide an ongoing management framework. This process progressively documents issues and tracks how items are resolved, providing the client or owner with a transparent outcome that clearly outlines their ongoing maintenance responsibilities.
Progressively, we have been conducting SID reviews in a live 3D environment. This has provided an avenue to tackle one of the biggest challenges of the Safety in Design process: practically involving all stakeholders. Two-dimensional drawings are abstract in nature, and so reading plans and specifications can be difficult if you are not a builder or engineer who uses them everyday. An immersive 3D environment allows end users, operators and maintenance staff to gain an appreciation of what needs maintaining and in particular, what access is required to efficiently maintain all active equipment. Conducting the SID review in this interactive manner provides the project team with instant visual feedback, allowing us to jointly identify any potential safety issues in real-time.
On a recent processing project, we took the engineering team on a virtual walk through a crowded roof space to highlight concerns about the layout of client-provided installation work. This enabled re-engineering so that the right materials and workflow could be adopted, avoiding the need for re-work onsite. Maintenance strategies were also developed virtually – safe work practices were identified on the drawing board, and custom tools and gantries were integrated into the structure where necessary to allow safe manual handling.
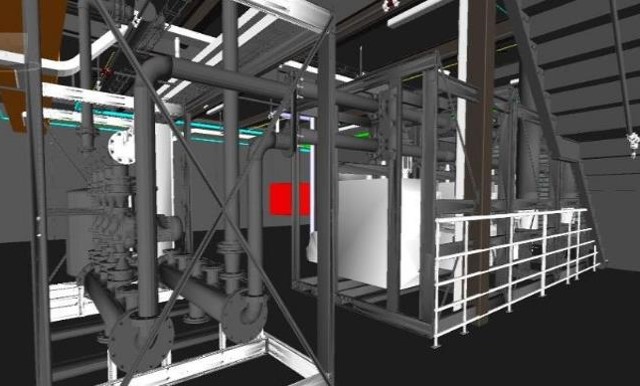
A capture of a 3D model of a processing plant
The way that this technology can quickly and easily involve multiple stakeholders in problem-solving at an early stage is invaluable. By contrast, encountering these issues later on a live operational site and shutting down even for just a couple of hours to rectify them can have catastrophic consequences for production.
At this stage, the 3D model can be enhanced into a Building Information Model (BIM) to serve as an important asset management tool once construction is finished. With the right development, it can be used to help proactively manage maintenance throughout the asset lifecycle. Asset owners are also better at understanding the value this BIM data creates when it is time to extend or refurbish – removing the guesswork out of what will be uncovered during the next phase of asset life.
Browse more BADGE Blog posts